La capabilité sert à quantifier l’aptitude d’un processus (compte tenu de ses limites naturelles) à produire à l’intérieur d’un intervalle de tolérance. L’étude des capabilités consiste à analyser l’adéquation des performances du moyen de production et son évolution dans le temps, par rapport à l’objectif de performance visé (valeur cible et intervalle de tolérance).
On distingue:
· La capabilité court-terme du processus, Cp, qui compare la dispersion naturelle du processus (sans action de causes spéciales) et l’intervalle de tolérance (IT): Cp = IT / 6σCT. C’est donc la capabilité du moyen de production si l’on arrive à stabiliser le moyen, c'est-à-dire à éliminer les causes spéciales occasionnant un étalement de sa dispersion.
· La performance long-terme du processus, Pp, qui prend en compte sur l’ensemble de population l’action des causes spéciales (occasionnant une dérive de la position moyenne du processus): Pp = IT / 6σLT. Elle traduit la qualité des produits livrés au client.
Cp et Pp vérifient: Pp ≤ Cp
On définit également un indicateur de déréglage long-terme, Ppk, ratio de la distance entre la moyenne sur toute la population (μ) et la limite de tolérance la plus proche (TS ou TI), divisée par 3 σLT: Pp = (μ-T)/3σLT.
Un processus est dit capable sur le long terme, c'est-à-dire susceptible de ne pas produire de pièces défectueuses, si Ppk > 1,33 (i.e., moins de 64 pièces défectueuses par million pour un processus centré tel que Ppk=Pp=1,33).
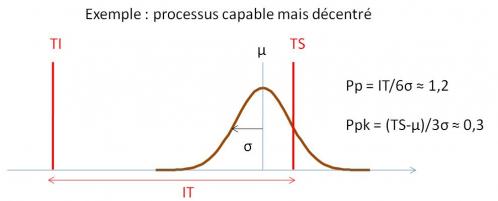
Ainsi, un processus part d’un potentiel de capabilité égal à Cp. La chute de capabilité de Cp à Pp traduit l’instabilité du processus (c'est-à-dire l’étalement de sa dispersion avec le temps parce que la machine ne tient pas la consigne sur la valeur cible et que ces écarts ne sont pas corrigés) alors que la chute de capabilité de Pp à Ppk est due au déréglage du processus sur le long terme (écart de la moyenne par rapport à la cible).
L’étude de cette « chute des capabilités » est un outil puissant de l’approche 6-sigma pour améliorer très sensiblement le taux de qualité d’un processus de production.
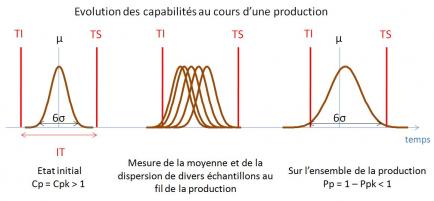
Voir l'ensemble des billets du BLOG